Switchgrass (Panicum virgatum) is a native warm-season grass that is a leading biomass crop in the United States. More than 70 years of experience with switchgrass as a hay and forage crop suggest switchgrass will be productive and sustainable on rain-fed marginal land east of the 100th meridian. Long-term plot trials and farm-scale studies in the Great Plains and plot trials in the Great Plains, Midwest, South, and Southeast indicate switchgrass is productive, protective of the environment, and profitable for the farmer. Weed control is essential during establishment but with good management is typically not required again. Although stands can be maintained indefinitely, stands are expected to last at least 10 years, after which time the stand will be renovated, and new, higher-yielding material will be seeded on the site. Fertility requirements are well understood in most regions, with about 12 to 14 pounds of N per acre required for each ton of expected yield if the crop is allowed to completely senesce before the annual harvest. Historically, breeding and genetics research has been conducted at a limited number of locations by USDA and university scientists, but the potential bioenergy market has promoted testing by public and private entities throughout the United States. Switchgrass is well suited to marginal cropland and is an energetically and economically feasible and sustainable biomass energy crop with currently available technology.
Table of Contents
- Introduction
- Current Potential for Use as a Biofuel
- Biology and Adaptation
- Production and Agronomic Information
- Potential Yield
- Production Challenges
- Production Cost
- Environmental and Sustainability Issues
- Feasibility
- Summary
- Bibliography
- Contributors to This Article
Introduction
Grassland scientists have conducted research on switchgrass (Panicum virgatum) for more than 70 years, with initial research focusing on livestock and conservation. In 1936, L. C. Newell, an agronomist with the Bureau of Plant Industry, USDA, in Lincoln, Nebraska, began working with switchgrass and other grasses to potentially re-vegetate large areas of the central Great Plains and Midwest that had been devastated by the drought of the 1930s. The first switchgrass cultivar from this program was Nebraska 28 which was jointly released by USDA and the University of Nebraska in 1949. Since that time, establishment and management practices have been developed and refined, genetic resources have been evaluated, seed production has been improved, and a wealth of information has been made available to producers.
Most of the general public first heard about switchgrass on January 31, 2006, when President George W. Bush in his State of the Union Address said, “We must also change how we power our automobiles. We will increase our research in better batteries for hybrid and electric cars, and in pollution-free cars that run on hydrogen. We’ll also fund additional research in cutting-edge methods of producing ethanol, not just from corn, but from wood chips and stalks, or switchgrass. Our goal is to make this new kind of ethanol practical and competitive within six years.” Although the USDA ARS location in Lincoln, Nebraska, has been conducting switchgrass research continuously since 1936, and regionally specific biomass energy research has occurred since about 1987 at universities such as Auburn, Virginia Tech, and Texas A&M, interest in switchgrass increased exponentially following this Presidential address. Recently, significant attention has been given to switchgrass as a model perennial grass for bioenergy production to reduce our dependence on foreign oil, boost our rural economies, reduce fossil fuel emissions, reduce erosion on marginal cropland, and enhance wildlife habitat.
Current Potential for Use as a Biofuel
Switchgrass has excellent potential as a bioenergy feedstock for cellulosic ethanol production, direct combustion for heat and electrical generation, gasification, and pyrolysis. The U.S. Department of Energy (DOE) Bioenergy Feedstock Development Program selected switchgrass as the herbaceous model species for biomass energy. Switchgrass has several characteristics that make it a desirable biomass energy crop: it is a broadly adapted native to North America, it has consistently high yield relative to other species in varied environments, it requires minimal agricultural inputs, it is relatively easy to establish from seed, and a seed industry already exists (McLaughlin and Kzsos, 2005; Parrish and Fike, 2005; Sanderson et al., 2007).
Biology and Adaptation
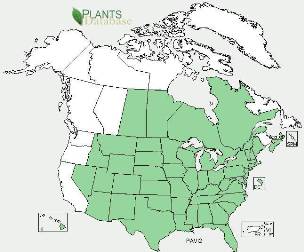
Switchgrass is a perennial warm-season (C4) grass that is native to most of North America except for areas west of the Rocky Mountains and north of 55°N latitude (Figure 1). Switchgrass grows 3 to 10 feet tall, typically as a bunchgrass, but the short rhizomes can form a sod over time. Switchgrass has high yield potential on marginal cropland and will be productive in most rain-fed production systems east of the 100th meridian (Vogel, 2004). Productive switchgrass stands can be grown west of the 100th meridian with irrigation (Biofuels Cropping Systems Research and Extension, Washington State University). Switchgrass is adapted to a wide range of habitats and climates and has few major insect or disease pests. Root depth of established switchgrass may reach 10 feet, but most of the root mass is in the top 12 inches of the soil profile. In addition to potential bioenergy production, switchgrass uses include pasture and hay production, soil and water conservation, carbon sequestration, and wildlife habitat.
Lowland vs Upland Ecotypes
Switchgrass has distinct lowland and upland ecotypes. Upland ecotypes occur in upland areas that are not subject to flooding, whereas lowland ecotypes are found on floodplains and other areas that receive run-on water (Vogel, 2004). Generally, lowland plants have a later heading date and are taller with larger and thicker stems. Upland ecotypes are either octaploids or tetraploids, whereas lowland ecotypes are tetraploids (Vogel, 2004). Lowland and upland tetraploids have been crossed to produce true F1 hybrids that have a 30 to 50% yield increase over the parental lines (Vogel and Mitchell, 2008). These hybrids are promising sources for high-yielding bioenergy cultivars.
Production and Agronomic Information
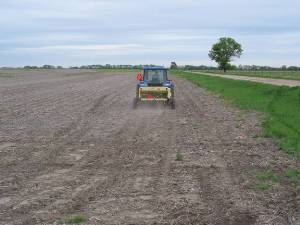
Establishing Stands
Successful stand establishment during the seeding year is mandatory for economically viable switchgrass bioenergy production systems (Perrin et al., 2008). Weed competition is the major reason for switchgrass stand failure. Acceptable switchgrass production can be delayed by one or more years by weed competition and poor stand establishment (Schmer et al., 2006). Vogel and Masters (2001) reported a stand frequency of 50% or greater (two or more switchgrass plants per square foot) indicated a successful stand, whereas stand frequency from 25 to 50% was marginal to adequate, and stands with less than 25% frequency indicated a partial stand. In a study conducted on 12 farms in Nebraska, South Dakota, and North Dakota, switchgrass fields with a stand frequency of 40% or greater provided a successful stand (Schmer et al., 2006).
Switchgrass is readily established when quality seed of an adapted cultivar is used with the proper planting date, seeding rate, seeding method, and weed control. In the central Great Plains, switchgrass can be planted two or three weeks before to two or three weeks after the recommended planting dates for corn (Zea mays), typically from late April to early June. Switchgrass should be seeded at 30 pure live seed (PLS) per square foot (5 PLS pounds per acre) based on the quality of the seedlot. Excellent results are obtained by planting after a soybean (Glycine max) crop using a properly calibrated no-till drill with depth bands that plant seeds 0.25 inch to 0.5 inch deep followed by press wheels (Figure 2). Row spacing for switchgrass is typically 7.5 to 10 inches. If switchgrass is planted after crops that leave heavy residue such as corn or sorghum (Sorghum bicolor), it may be necessary to graze the residue, shred or bale the stalks, or use tillage to reduce the residue. If tillage is required, the seedbed needs to be packed to firm the soil. The packed soil needs to be firm enough so that walking across the field leaves only a faint footprint (Figure 3). Applying 8 oz of quinclorac plus 1 qt of atrazine per acre immediately after planting has provided effective grassy and broadleaf weed control for establishment. The most cost-effective method to control broadleaf weeds in switchgrass fields during the establishment year is to apply 2,4-D at 1 to 2 qt acre-1 after switchgrass seedlings have about four leaves. After the establishment year, a successfully established switchgrass stand requires limited herbicide applications.
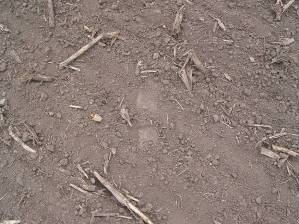
Nitrogen (N) fertilizer is not recommended during the planting year since N will encourage weed growth, increase competition for establishing seedlings, increase establishment cost, and increase economic risk associated with establishment if stands should fail (Mitchell et al., 2008). Soil tests are recommended prior to planting. Since switchgrass is deep rooted, soil samples should be taken from each 1-foot increment to a depth of 5 feet. In most agricultural fields, adequate levels of phosphorus (P) and potassium (K) will be in the soil profile. If warranted by soil tests, P and K can be applied before seeding to encourage root growth and promote rapid establishment. Recommended P levels for the western corn belt are in Table 1. Switchgrass can tolerate moderately acidic soils, but optimum seed germination occurs when soil pH is between 6 and 8 (Hanson and Johnson, 2005). With good weed management and favorable precipitation, a crop equal to about half of potential production can be harvested after frost at the end of the planting year, with 75 to 100% of full production achieved the year after planting.
Table 1. Phosphorus (P) recommendations for the western corn belt based on two common soil test levels (Anderson and Shapiro, 1990).
|
Soil Test Levels |
|
|
P Index Value |
Bray & Kurtz #1 |
Olsen P (Na HCO3) |
P Rate |
|
———- ppm ———- |
lb P2O5/Acre |
|
Very low |
0-5 |
0-3 |
40 |
Low |
6-15 |
4-7 |
20 |
Medium |
16-25 |
8-14 |
10 |
High |
25+ |
15+ |
0 |
Established Stands
Although switchgrass can survive on low fertility soils, it does respond to fertilizer, especially N. The amount of N required by switchgrass is a function of the yield potential of the site, productivity of the cultivar, and other management practices being used (Vogel et al., 2002). Consequently, the optimum N rate for switchgrass managed for biomass will vary, but a few references indicative of the responses to N in different regions of the United States are included (Table 2). Additionally, biomass will decline over years if inadequate N is applied, and yield will be sustainable only with proper N application (Muir et al., 2001). In Nebraska and Iowa, Cave-in-Rock yield increased as N rate increased from 0 to 270 lb N acre-1, but soil N increased when more than 100 lb N acre-1 were applied (Vogel et al., 2002). They reported biomass was optimized by applying 100 lb N acre-1, with about the same amount of N being applied as was being removed by the crop. A general N fertilizer recommendation for the Great Plains and Midwest region is to apply 20 lb N acre-1 yr-1 for each ton of anticipated biomass if harvesting during the growing season, with N rate reduced to 12 to 14 lb N acre-1 yr-1 for each ton of anticipated biomass if harvesting after a killing frost. The N rate can be reduced when the harvest is after a killing frost because switchgrass cycles some N back to roots during autumn. If soil tests indicate a new switchgrass field has high residual N levels, N rates can be significantly reduced during the initial production years using the above information as a guideline. Apply N at switchgrass green-up to minimize cool-season weed competition.
Table 2. Switchgrass publications addressing nitrogen fertilizer application for different regions of the United States listed by state, the major parameters evaluated in the study, and references for each study.
State(s) |
Parameters Evaluated |
Reference |
AL |
N rate and row spacing effect on C partitioning |
Ma et al., 2001 |
IA |
Yield and quality parameters for 20 strains |
Lemus et al., 2002 |
IA, NE |
Harvest date and N rate effects |
Vogel et al., 2002 |
NC, KY, TN, VA, WV |
Long-term yield under different management regimes |
Fike et al., 2006a |
SD |
Harvest date and N rate effects on biomass, persistence, species composition, and soil organic carbon of switchgrass-dominated CRP |
Mulkey et al., 2006 |
TX |
Yield and stand responses to N and P as affected by row spacing |
Muir et al., 2001 |
Spraying herbicides to control broadleaf weeds typically is needed only once or twice every 10 years in an established, well-managed switchgrass stands. When needed, the most effective and economical approach is with broadcast applications of 2,4-D at 1 to 2 qt acre-1. Spray broadleaf weeds as early in the growing season as possible to reduce the impact of weed interference on switchgrass yield. In some cases, cool-season grasses may invade switchgrass stands and reduce yield. Harvesting after switchgrass senescence in autumn but while cool-season grasses are growing, then applying glyphosate at 1 to 2 qt acre-1, is an effective method to reduce cool-season grasses. However, make certain switchgrass is dormant when glyphosate is applied, or stands could be damaged. Spring applications of atrazine at 2 qt acre-1 can be used to control cool-season grasses in established switchgrass stands.

Harvest and Storage
Maximizing yield currently is the primary objective when harvesting biomass feedstocks. In the Great Plains and Midwest, maximum first-cut yields are attained by harvesting switchgrass when panicles are fully emerged to the post-anthesis stage (~1 August). Sufficient regrowth may occur about one year out of four to warrant a second harvest after a killing frost. Do not harvest switchgrass within six weeks of the first killing frost or shorter than a 4-inch stubble height to ensure translocation of storage carbohydrates to maintain stand productivity and persistence. Dormant season harvests after a killing frost will not damage switchgrass stands but will reduce the amount of snow captured during winter. In general, a single harvest during the growing season maximizes switchgrass biomass recovery, but harvesting after a killing frost will ensure stand productivity and persistence, especially when drought conditions occur, and reduce N fertilizer requirements. Delaying harvest until spring will reduce moisture and ash contents, but yield loss can be as high as 40% compared with a fall harvest (Adler et al., 2006). With proper management, productive stands can be maintained indefinitely and certainly for more than 10 years. Harvesting switchgrass in summer at or after flowering when drought conditions exist is not recommended.
Switchgrass can be harvested and baled with commercially available haying equipment. Self-propelled harvesters equipped with a rotary head (disc mowers) have most effectively harvested high-yielding (>6-ton per acre) switchgrass fields (Figure 4). Additionally, after a killing frost, the multidirectional arrangement of the switchgrass in the windrow was easier to bale than the linearly arranged windrow left by a sickle-bar head. Round bales tend to have less storage losses than large square bales (>800 lb) when stored outside, but square bales tend to be easier to handle and load a truck for transport without road width restrictions (Figure 5). After harvest, poor switchgrass storage conditions can result in storage losses of 25% in a single year. In addition to storage losses in weight, there can be significant reductions in biomass quality, and the biomass may not be in acceptable condition for a biorefinery. Switchgrass grown for use in a biorefinery may have to be stored for a full year or longer since biorefineries will operate 365 days a year. Some type of covered storage will be necessary to protect the producer’s investment.
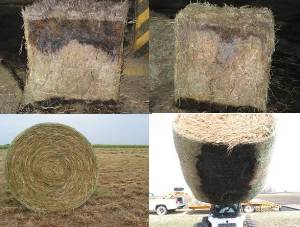
Potential Yield
Switchgrass yield is strongly influenced by precipitation, fertility, soil, location, genetics, and other factors. Most plot and field-scale switchgrass research has been conducted on forage-type cultivars selected for other livestock-based characteristics in addition to yield. Consequently, the forage-type cultivars in the Great Plains and Midwest are entirely represented by upland ecotypes which are inherently lower yielding than lowland ecotypes. Thus, yield data comparing forage-type upland cultivars like Cave-In-Rock, Shawnee, Summer, and Trailblazer do not capture the full yield potential of switchgrass and are not fair comparisons. For example in Nebraska, high-yielding F1 hybrids of Kanlow and Summer produced 9.4 tons acre-1 year-1, which was 68% greater than Summer and 50% greater than Shawnee (Vogel and Mitchell, 2008). New biomass-type switchgrass cultivars will be available in the near future for the Great Plains and Midwest. Knowing the origin of a switchgrass cultivar is important since switchgrass is photoperiod sensitive. Planting a switchgrass cultivar too far north of the cultivar origin area (>300 miles) can result in winter stand loss. Planting a switchgrass cultivar south of its origin area results in less biomass because the shorter photoperiod causes plants to flower too early.
Production Challenges
There are major challenges to using switchgrass for cellulosic ethanol (Mitchell et al., 2008). An ethanol plant requires a reliable and consistent feedstock supply. A 50-million-gallon per year plant will require 625,000 U.S. tons of feedstock per year assuming 80 gallons of ethanol can be produced from one ton of feedstock. Although cellulosic ethanol plants likely will use multiple feedstocks, this example assumes switchgrass will be the only feedstock. Operating every day of the year, the plant will require 1,712 dry matter (DM) tons of feedstock per day, or 342 acres of switchgrass yielding 5 DM tons per acre. If a loaded semi can deliver 30 round bales each containing 0.6 DM tons (18 U.S. tons), the ethanol plant will use 95 semi loads of feedstock per day, requiring a semi to be unloaded every 15 minutes 24 hours per day, 7 days per week.
There must be an available land base in the local agricultural landscape to produce feedstock. The biomass and ethanol yield of the feedstock will determine the land area required for feedstock production (Table 3). Assuming 25 miles is the maximum economically feasible distance feedstock can be transported, all of the feedstock must be grown within a 25-mile radius of the bio-refinery, an area containing about 1.26 million acres. Assuming a 50-million-gallon per year cellulosic ethanol plant requires 625,000 tons of feedstock per year, if feedstock yield is 1.75 DM tons/acre, 28% of the land would need to grow the feedstock, and this is not feasible in most agricultural areas. At 5 DM tons/acre, a commonly-achieved yield with available forage cultivars, only 10% of the land would be needed for feedstock production and is feasible in most agricultural areas. However, at 10 DM tons/acre, only 5% of the land base would be needed for feedstock production and would minimally alter the agricultural landscape. Dry matter yield will exceed 10 tons/acre in many areas of the South and Southeast, so less than 5% of the land base would be needed for feedstock production. This example reinforces the importance of high DM yield to the agricultural feasibility of cellulosic ethanol, not to mention the inability of the producer to profit by growing low-yielding energy crops. A majority of the switchgrass likely will be grown on marginal lands that have suboptimal characteristics (i.e., slope, soil depth, etc.) for producing food and feed, or on lands currently enrolled in conservation programs.
Table 3. Reported dry matter (DM) yield, acres required to grow 625,000 tons of dry matter per year, and the percent of the land base required to provide feedstock for a 50-million-gallon cellulosic ethanol plant for different herbaceous perennial feedstocks in the Great Plains and Midwest.
Feedstock |
Yield, DM tons/acre |
Acres needed to grow 625,000 DM tons/year |
Percent of land in 25-mile radius |
LIHD prairie1 |
1.75 |
357,000 |
28 |
Managed native prairie2 |
2.5 |
250,000 |
20 |
Shawnee switchgrass3 |
5 |
125,000 |
10 |
Bioenergy switchgrass4 |
7.4 |
84,460 |
6.6 |
Hybrid switchgrass5 |
9.4 |
66,489 |
5.3 |
1Low-input, high-diversity human-made prairies (Tilman et al., 2006).
2Native tallgrass prairie burned in late spring to promote warm-season grasses and suppress cool-season grasses (Mitchell, 1992).
3Shawnee is an upland forage-type switchgrass cultivar released in 1995.
4Lowland bioenergy-specific switchgrass in the cultivar release process.
5F1 hybrid of Summer and Kanlow switchgrass that will likely reach field-scale production in less than 10 years (Vogel and Mitchell, 2008).
Growing switchgrass must be profitable for the producer, it must fit into existing farming operations, it must be easy to store and deliver to the ethanol plant, and extension efforts must be provided to inform producers on the agronomics and best management practices for specific regions, all of which have been addressed for switchgrass. Switchgrass fits well into the production systems of most farmers. Harvesting switchgrass after frost is a time when most farmers have completed corn and soybean harvests and handling switchgrass as a hay crop is not foreign to most producers. The economic opportunities of switchgrass for small, difficult-to-farm, or poorly-productive fields will be attractive to many producers.
There are potential difficulties with large-scale switchgrass monocultures, but most are speculation at this point. Concerns arise for potential disease and insect pests, and the escape of switchgrass as an invasive species with the production of millions of switchgrass acres, especially since little research has been conducted on these topics. Most pathogen issues cannot be fully realized until large areas are planted to switchgrass. However, the broad genetic diversity available to switchgrass breeders, the initial pathogen screening conducted during cultivar development, and the fact that switchgrass has been a native component of central U.S. grasslands for centuries will likely limit the negative pest issues. Switchgrass has been used widely throughout the Great Plains and Midwest for pasture and conservation purposes for decades, and no invasive problems have developed or been identified.
Production Cost
Results of a recent economic study based on the five-year average of 10 farms in Nebraska, South Dakota, and North Dakota indicated producers can grow switchgrass at a farm gate cost of $60/ton (Perrin et al., 2008). However, producers with experience growing switchgrass had five-year average costs of $43/ton, and one producer grew switchgrass for $38/ton. These costs include all expenses plus land costs and labor at $10/hour. Each big round bale (Photo 4) represents 50 gallons of ethanol assuming 80 gallons per ton of switchgrass, with a farm gate cost of $0.75/gallon at $60/ton. This research from nearly 50 production environments indicates that growing switchgrass for cellulosic ethanol is economically feasible in the central and northern Great Plains. It should be noted that fuel and land prices have increased since this study, so the cost increases for those inputs need to be considered when determining switchgrass production costs.
Environmental and Sustainability Issues
Sustainable biomass energy crops must be productive, protective of soil and water resources, and profitable for the producer. Numerous studies have reported that switchgrass will protect soil, water, and air quality; provide fully sustainable production systems; sequester C; create wildlife habitat; increase landscape and biological diversity; return marginal farmland to production; and increase farm revenues (McLaughlin and Walsh, 1998; McLaughlin et al., 2002). Switchgrass root density in the surface 6 inches is two-fold greater than alfalfa, more than three-fold greater than corn, and more than an order of magnitude greater than soybean (Johnson et al., 2007). In a five-year field study conducted on 10 farms in Nebraska, South Dakota, and North Dakota, Liebig et al. (2008) reported that switchgrass stored large quantities of C, with four farms in Nebraska storing an average of 2,590 pounds of soil organic C (SOC) acre-1 year-1 when measured to a depth of 4 feet. However, they noted that SOC increases varied across sites, and the variation in SOC change reiterated the importance of long-term environmental monitoring sites in major agro-ecoregions.
Energy produced from renewable carbon sources is held to a different standard than energy produced from fossil fuels, in that renewable fuels must have highly positive energy values and low greenhouse gas emissions. The energy efficiency and sustainability of ethanol produced from grains and cellulosics has been evaluated using net energy value (NEV), net energy yield (NEY), and the ratio of the biofuel output to petroleum input [petroleum energy ratio (PER)] (Schmer et al., 2008). An energy model using estimated agricultural inputs and simulated yields predicted switchgrass could produce greater than 700% more output than input energy (Farrell et al., 2006). These modeled results were validated with actual inputs from multi-farm, field-scale research to predict energy output. Switchgrass fields on 10 farms in Nebraska, South Dakota, and North Dakota produced 540% more renewable energy (NEV) than nonrenewable energy consumed over a five-year period (Schmer et al., 2008). The estimated on-farm NEY was 93% greater than human-made prairies and 652% greater than low-input switchgrass grown in small plots in Minnesota (Tilman et al., 2006). The 10 farms and five production years had a PER of 13.1 and produced 93% more ethanol per acre than human-made prairies and 471% more ethanol per acre than low-input switchgrass in Minnesota (Schmer et al., 2008). Average greenhouse gas (GHG) emissions from switchgrass-based ethanol were 94% lower than estimated GHG emissions for gasoline (Schmer et al., 2008). Switchgrass for bioenergy is an energetically positive and environmentally sustainable production system for the Great Plains.
Implementing switchgrass-based bioenergy production systems will require converting marginal land from annual row crops to switchgrass and could exceed 10% in some regions depending on the yield potential of the switchgrass strains (Table 3). In a five-year study in Nebraska, the potential ethanol yield of switchgrass averaged 372 gallons acre-1 and was equal to or greater than that for no-till corn (grain + stover) on a dry-land site with marginal soils (Varvel et al., 2008). Removing 50% of the corn stover each year reduced subsequent corn grain yield, stover yield, and total biomass. Growing switchgrass on marginal sites likely will enhance ecosystem services more rapidly and significantly than on more productive sites.
Feasibility
Perennial herbaceous energy crops provide several challenges. A stable and consistent feedstock supply must be available year-round to the ethanol or power plant. For the producer, perennial herbaceous energy crops must be profitable, they must fit into existing farming operations, they must be easy to store and deliver to the plant, and extension efforts must be provided to inform producers on the agronomics and best management practices for growing perennial herbaceous energy crops. However, perennial herbaceous energy crops have potential for improvement, and they present a unique opportunity for cultural change on the agricultural landscape. There are numerous environmental benefits to perennial herbaceous cropping systems that can improve agricultural land use practices such as stabilizing soils and reducing soil erosion, improved water quality, increased and improved wildlife habitat, and storing C to mitigate greenhouse gas emissions. There is large potential for achieving all of these benefits, provided agronomic, genomic, and operational aspects of perennial herbaceous cropping systems are fully developed and accepted by farmers. Herbaceous perennial energy crops may be used in conjunction with agriculture residues (corn stover and wheat straw), which likely would be harvested in autumn, and perennial grasses could be harvested in very early spring while they are dry, similar to when prairies are typically burned. This may help reduce the need for feedstock storage by providing feedstock at different times during the year.
Growing seed to meet potential demand for bioenergy will not be an issue. Switchgrass has many desirable seed characteristics and can produce viable seed during the seeding year, especially under irrigation. Established seed production fields can produce 500 to 1,000 pounds of seed per acre with irrigation, and the seed is easily threshed, cleaned, and planted with commercial planting equipment. Seed production systems are well established (Cornelius, 1950), and a commercial industry for switchgrass seed has existed for over 50 years.
Summary
Contrary to popular belief, switchgrass is not a new or novel crop but has more than 70 years of research and farming experience. Currently available plant materials and production practices can reliably produce five tons per acre in the central Great Plains and Midwest and 10 tons per acre in much of the Southeast. New cultivars and management practices will significantly increase yields similar to the yield increases achieved in corn in the last 30 years. The availability of adequate acres of agricultural land and the profit potential provided to farmers for growing switchgrass in a region will determine the success of growing switchgrass for biomass energy. Production practices and plant materials are available to achieve sustainable and profitable biomass production, for both farmers and bio-refineries, to help meet the energy requirements of the nation and reduce our dependence on foreign oil.
Bibliography
- Adler, P.R., M.A. Sanderson, A.A. Boeteng, P.J. Weimer, P.B. Adler, and H.G. Jung. 2006. Biomass yield and biofuel quality of switchgrass harvested in fall or spring. Agron. J. 98:1518-1528.
- Anderson, B., and C. Shapiro. 1990. Fertilizing grass pastures and haylands. Univ. of Nebraska-Lincoln Extension, IANR NebGuide G78-406-A.
- Cornelius, D.R. 1950. Seed production of native grasses. Ecol. Mono. 20:1-27.
- Davison, J. 1999. Switchgrass varieties for western Nevada. Univ. of Nevada, Reno Cooperative Extension Fact Sheet 99-65.
- Farrell, A.E., R.J. Plevin, B.T. Turner, A.D. Jones, M. O’Hare, and D.M. Kammen. 2006. Ethanol can contribute to energy and environmental goals. Science 311:506-508.
- Fike, J., D. Parrish, D. Wolf, J. Balasko, J. Green Jr., M. Rasnake, and J. Reynolds. 2006a. Long-term yield potential of switchgrass-for-biofuel systems. Biomass Bioenergy 30:198-206.
- Fike, J., D. Parrish, D. Wolf, J. Balasko, J. Green Jr., M. Rasnake, and J. Reynolds. 2006b. Switchgrass production for the upper southeastern USA: Influence of cultivar and cutting frequency on biomass yields. Biomass Bioenergy 30:207-213.
- Hanson, J.D., and H. A. Johnson. 2005. Germination of switchgrass under various temperature and pH regimes. Seed Tech. 27:203-210.
- Johnson, J.M.F., N.W. Barbour, and S.L. Weyers. 2007. Chemical composition of crop biomass impacts its decomposition. Soil Sci. Soc. Am. J. 71:155-162.
- Lee, D.K., V.N. Owens, and J.J. Doolittle. 2007. Switchgrass and soil carbon sequestration response to ammonium nitrate, manure, and harvest frequency on Conservation Reserve Program land. Agron. J. 99:462-468.
- Lemus, R., E.C. Brummer, K.J. Moore, N.E. Molstad, C.L. Burras, and M. Barker. 2002. Biomass yield and quality of 20 switchgrass populations in southern Iowa, USA. Biomass and Bioenergy 23:433-442.
- Liebig, M.A., M.R. Schmer, K.P. Vogel, and R.B. Mitchell. 2008. Soil carbon storage by switchgrass grown for bioenergy. BioEnergy Research 1:215-222.
- Ma, Z., C.W. Wood, and D.I. Bransby. 2001. Impact of row spacing, nitrogen rate, and time on carbon portioning of switchgrass. Biomass and Bioenergy 20:413-419.
- McLaughlin, S.B., D.G. De La Torre Ugarte, C.T. Garten Jr., L.R. Lynd, M.A. Sanderson, V.R. Tolbert, and D.D. Wolf. 2002. High-value renewable energy from prairie grasses. 2002. Environ. Sci. Technol. 36:2122-2129.
- McLaughlin, S.B., and L.A. Kszos. 2005. Development of switchgrass (Panicum virgatum) as a bioenergy feedstock in the United States. Biomass and Bioenergy 28:515-535.
- McLaughlin, S.B., and M.E. Walsh. 1998. Evaluating the environmental consequences of producing herbaceous crops for bioenergy. Biomass and Bioenergy 14:317-324.
- Mitchell, R.B. 1992. Influence of spring burning date, fertilization, and atrazine application on eastern Nebraska tallgrass prairies. M.S. Thesis, Univ. of Nebraska-Lincoln. 130 pages.
- Mitchell, R.B., and B.E. Anderson. 2008. Switchgrass, big bluestem, and indiangrass for grazing and hay. Univ. of Nebraska-Lincoln Extension, IANR NebGuide G1908. (http://www.ianrpubs.unl.edu/epublic/live/g1908/build/g1908.pdf)
- Mitchell, R.B., K.P. Vogel, and G. Sarath. 2008. Managing and enhancing switchgrass as a bioenergy feedstock. Biofuels, Bioproducts, & Biorefining 2:530-539.
- Muir, J.P., M.A. Sanderson, W.R. Ocumpaugh, R.M. Jones, and R.L. Reed. 2001. Biomass production of ‘Alamo’ switchgrass in response to nitrogen, phosphorus, and row spacing. Agron. J. 93:896-901.
- Mulkey, V.R., V.N. Owens, and D.K. Lee. 2006. Management of switchgrass-dominated Conservation Reserve Program lands for biomass production in South Dakota. Crop Sci. 46:712-720.
- Parrish, D.J., and J.H. Fike. 2005. The biology and agronomy of switchgrass for biofuels. Critical Reviews in Plant Sciences 24:423-459.
- Perrin, R.K., K.P. Vogel, M.R. Schmer, and R.B. Mitchell. 2008. Farm-scale production cost of switchgrass for biomass. BioEnergy Research 1:91-97.
- Sanderson, M.A., P.R. Adler, A.A. Boateng, M.D. Casler, and G. Sarath. 2007. Switchgrass as a biofuels feedstock in the USA. Can. J. Plant Sci. 86:1315-1325.
- Sanderson, M.A., R. Reed, S. McLaughlin, S. Wullschleger, B. Conger, D. Parrish, D. Wolf, C. Taliaferro, A. Hopkins, W. Ocumpaugh, M. Hussey, J. Read, and C. Tischler. 1996. Switchgrass as a sustainable bioenergy crop. Bioresource Technology 56:83–93.
- Schmer, M.R., K.P. Vogel, R.B. Mitchell, L.E. Moser, K.M. Eskridge, and R.K. Perrin. 2006. Establishment stand thresholds for switchgrass grown as a bioenergy crop. Crop Sci. 46:157-161.
- Schmer, M.R., K.P. Vogel, R.B. Mitchell, and R.K. Perrin. 2008. Net energy of cellulosic ethanol from switchgrass. Proc. National Acad. Sci. 105:464-469.
- Tilman, D., J. Hill, and C. Lehman. 2006. Carbon-negative biofuels from low-input high-diversity grassland biomass. Science 314:1598-1600.
- Varvel, G.E., K.P. Vogel, R.B. Mitchell, R.N. Follett, and J.M. Kimble. 2008. Comparison of corn and switchgrass on marginal soils for Bioenergy. Biomass and Bioenergy 32:18-21.
- Vogel, K.P. 2004. Switchgrass. p. 561-588 In: L.E. Moser et al., eds. Warm-season (C4) Grasses. ASA-CSSA-SSSA, Madison, WI.
- Vogel, K.P., J.J. Brejda, D. T. Walters, D.R. Buxton. 2002. Switchgrass biomass production in the Midwest USA: Harvest and nitrogen management. Agron. J. 94:413-420.
- Vogel, K.P., and R.A. Masters. 2001. Frequency grid – A simple tool for measuring grassland establishment. J. Range Manage. 54:653-655.
- Vogel, K.P., and R.B. Mitchell. 2008. Heterosis in switchgrass: Biomass yield in swards. Crop Sci. 48:2159-2164.
In-depth Reviews
- Casler, M., E. Heaton, K. Shinners, H. Jung, P. Weimer, M. Liebig, and R. Mitchell. 2009. Grasses and legumes for cellulosic bioenergy. pp. 205-219. In: W.F. Wedin, and S.L. Fales, eds. Grassland: Quietness and Strength for a New American Agriculture. ASA-CSSA-SSSA, Madison, WI.
- McLaughlin, S.B., and L.A. Kszos. 2005. Development of switchgrass (Panicum virgatum) as a bioenergy feedstock in the United States. Biomass and Bioenergy 28:515-535.
- Mitchell, R.B., K.P. Vogel, and G. Sarath. 2008. Managing and enhancing switchgrass as a bioenergy feedstock. Biofuels, Bioproducts, and Biorefining 2:530-539.
- Parrish, D.J., and J.H. Fike. 2005. The biology and agronomy of switchgrass for biofuels. Critical Reviews in Plant Sciences 24:423-459.
- Sanderson, M.A., P.R. Adler, A.A. Boateng, M.D. Casler, and G. Sarath. 2007. Switchgrass as a biofuels feedstock in the USA. Can. J. Plant Sci. 86:1315-1325.
- Sanderson, M.A., R. Reed, S. McLaughlin, S. Wullschleger, B. Conger, D. Parrish, D. Wolf, C. Taliaferro, A. Hopkins, W. Ocumpaugh, M. Hussey, J. Read, and C. Tischler. 1996. Switchgrass as a sustainable bioenergy crop. Bioresource Technology 56:83–93.
- Vogel, K.P. 2004. Switchgrass. pp. 561-588 In: L.E. Moser et al., eds. Warm-season (C4) Grasses. ASA-CSSA-SSSA, Madison, WI.
Additional Switchgrass Resources
- CenUSA Resources – Sustainable Production and Distribution of Bioenergy for the Central USA. Includes fact sheets and media resources on switchgrass development, production, logistics, harvesting, etc.
- Switchgrass as a Bioenergy Crop. ATTRA Publication No. IP302
- Goat Pastures Switchgrass
- Switchgrass. Sun Grant Bioweb
- Switchgrass Bioenergy Budgets. Rutgers NJAES Cooperative Extension
- Economic Potential of Switchgrass as a Biofuel Crop in Florida. University of Florida IFAS Extension
Contributors to This Article
Authors
- Rob Mitchell, USDA-ARS Grain, Forage, and Bioenergy Research Unit, Lincoln, NE
- Ken Vogel, USDA-ARS Grain, Forage, and Bioenergy Research Unit, Lincoln, NE
- Marty Schmer, USDA-ARS Northern Great Plains Research Lab, Mandan, ND
Reviewers
- Dennis Pennington, Michigan State University Extension, Hickory Corners, MI 49060